Bronze
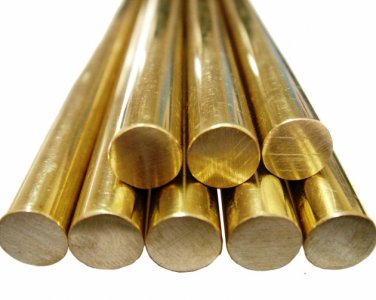
Le bronze est un alliage à base de cuivre et d'étain, avec du béryllium, de l’aluminium et d’autres éléments, le plus souvent du phosphore, de l’aluminium, du zinc et du plomb. Toutefois, le bronze ne peut pas être un alliage de cuivre et de zinc (dans ce cas, on obtient du laiton) ou un alliage de cuivre et de nickel.
Pertinence
Le bronze le plus connu est l'étain, un alliage de cuivre et d'étain (le cuivreest majoritaire). C’est l’un des premiers métaux maîtrisés par l’homme. Les hommes connaissent cette composition depuis l'âge du bronze antique. Le bronze a longtemps été un métal stratégique (jusqu'au XIXe siècle, les canons étaient coulés en bronze). C’est un métal qui possède des qualités remarquables telles que la dureté, la durabilité et la haute technologie. La découverte du bronze a ouvert de vastes horizons à l’homme. Pour connaître les prix des métaux non ferreux et acheter du bronze, vous pouvez consulter notre site web.
Propriétés
Le bronze d'étain est peu pressé, peu découpé et peu plié. C’est un métal de fonderie et ses qualités de coulée ne sont pas inférieures à celles des autres métaux. Le bronze se distingue par un faible retrait — 1 à 2%, le retrait du laiton et de la fonte étant de 1,6%, celui de l’acier de plus de 3%. C’est pourquoi le bronze est utilisé avec succès pour les moulages artistiques complexes. Il présente une résistance élevée à la corrosion et des propriétés antifriction. Il est utilisé dans l’industrie chimique pour la fabrication de raccords et comme matériau antifriction pour les pièces mobiles.
Nuances de bronze
Lesbronzes à l'étain peuvent être alliés au zinc, à l’aluminium, au nickel, au phosphore, au plomb, à l’arsenic et à d’autres métaux. L’ajout de zinc (maximum 11%) ne modifie pas les caractéristiques du bronze, mais le rend nettement moins cher.
Alliage | Fe | Ni | As | Cu | Pb | Zn | Р | Sn | Impuretés |
---|---|---|---|---|---|---|---|---|---|
BROF2−0,25 | ≤0.05 | ≤0,2 | --- | 96,7−98,98 | ≤0,3 | ≤0.3 | 0,02−0,3 | 1−2,5 | ≤0,3 |
Le bronze additionné de zinc est appelé «Admiralty Bronze» et résiste très bien à la corrosion dans l’eau de mer. Le plomb et le phosphore améliorent les propriétés antifriction du bronze. Le bronze d’aluminium est léger et possède une résistance spécifique élevée.
Si | Fe | Mn | Al | Cu | Pb | Zn | Р | Sn | Impuretés |
---|---|---|---|---|---|---|---|---|---|
≤0.1 | 2−4 | 1−2 | 9−11 | 82,3−88 | ≤0,03 | ≤0.5 | ≤0.01 | ≤0.1 | ≤0,7 |
Il est demandé dans l’ingénierie des transports. Sa conductivité électrique élevée est importante dans l'électrotechnique. Les pièces en bronze au béryllium ne produisent pas d'étincelles en cas de choc et sont utilisées dans les environnements explosifs.
Alliage | Fe | Si | Al | Cu | Pb | Zn | Be | Ni | Impuretés |
---|---|---|---|---|---|---|---|---|---|
BrB2 | ≤0.15 | ≤0,15 | ≤0,15 | 96,9−98 | ≤0,005 | --- | 1,8−2,1 | 0,2−0,5 | ≤0,6 |
Un certain nombre d’alliages de cuivre ne sont pas des bronzes. Les plus connus sont le laiton (alliage Cu+Zn) et le constantan (Cu+Ni).
Fourniture
Nous fournissons des laminés d’acier non ferreux et des alliages de bronze certifiés aux meilleurs prix. La spécification comprend des données sur la composition en pourcentage et les propriétés mécaniques des produits. Nous facilitons l’achat de produits semi-finis pour la production à grande échelle. Nous offrons des conditions favorables aux acheteurs au détail. Notre entreprise se distingue par un niveau de service élevé et une grande réactivité.
Acheter à un prix compétitif
Toute la production de métaux rares et non ferreux vendue par Evek GmbH est conforme aux normes de qualité GOST et internationales. Tous les produits en bronze peuvent être achetés dans les plus brefs délais. Une haute qualité, des prix raisonnables et une large gamme de produits déterminent le visage de notre entreprise. En devenant notre client régulier, vous pouvez compter sur un système de remises. La coopération avec nous vous aidera à réaliser tous vos projets d’ingénierie. Nous attendons vos commandes sur notre site web.
Bronzes
Les bronzes sont des alliages à base de cuivre contenant plus de 2,5% (en poids) de composants d’alliage.
Les bronzes ne doivent pas contenir plus de zinc que la somme des autres éléments d’alliage, sinon l’alliage sera classé comme laiton.
Les bronzes sont désignés par le principal élément d’alliage (aluminium, étain, etc.), mais aussi, dans certains cas, par deux ou trois éléments (étain-phosphore, étain-zinc, étain-zinc-plomb, etc.).
Bronzes sans étain
La liste récapitulative des bronzes sans étain traités sous pression selon les normes russes et de leurs alliages de bronze étrangers figure au tableau 1.
La liste récapitulative des bronzes sans saponine traités sous pression selon les normes nationales et de leurs alliages de bronze étrangers est présentée dans le tableau 1.
Bronzes faiblement alliés :
Nuance de bronze | Analogue américain | Analogue allemand | Analogue japonais | Remarque |
---|---|---|---|---|
BrSr0.1 | - | CuAg0.1 (2.1203) | - | argent (Ag) |
- | - | CuAg0.1P (2.1191) | - | argent (Ag) |
Bronze au tellure | С14500 | CuTeP (2.1546) | - | tellure (Te) |
- | C19600 | - | - | ferreux (Fe) |
- | C19200 | - | - | ferreux (Fe) |
- | C19500 | - | - | ferreux (Fe) |
- | C19400 | CuFe2P (2.1310) | - | ferrugineux (Fe) |
- | - | - | C1401 | autres |
BrMg0,3 | - | CuMg0,4 (2.1322) | - | autres |
- | C14200 | - | - | autres |
- | C14700 | CuSP (2.1498) | - | divers |
- | - | CuZn0,5 (2.0205) | - | autres |
- | - | CuMg0.4 (2.1322) | - | autres |
- | - | CuMg0.7 (2.1323) | - | autres |
- | C15100 | CuZr (2.1580) | - | autres — |
BrCr1 | - | - | - | autres |
- | C18400 | CuCrZr (2.1293) | - | autres — |
BrKd1 | - | - | - | autres |
- | - | CuPbIp (2.1160) | - | autres |
Bronzes d’aluminium :
Qualité bronze | Analogue américain | Identique à l’Allemagne | Identique au Japon | Remarque |
---|---|---|---|---|
BrA5 | C60800 | CuA15As (2.0918) | - | Al-Cu |
BrA7 | - | CuA18 (2.0920) | - | Al-Cu |
- | C61400 | CuAl8Fe3 (2.0932) | C6140 | Al-Fe-Cu |
- | C61300 | - | - | Al-Fe-Cu |
BrAJ9−4 | C62300 | - | - | Al-Fe-Cu |
Idem | C61900 | - | - | Al-Fe-Cu |
- | C62400 | - | - | Al-Fe-Cu |
БрАМц9−2 | - | CuA19Mn2 (2.0960) | - | Al-Mn-Cu |
БрАМц10−2 | - | - | - | Al-Mn-Cu |
- | С64200 | - | - | Al-Si-Cu |
- | С64210 | - | - | Al-Si-Cu |
BrAJMc10−3-1b5 | - | CuA10Fe3Mn2 (2.0936) | - | Al-Fe-Mn-Cu |
BrAZHN10−4-4 | C63000 | CuA110Ni5Fe4 (2.0966) | - | Al-Fe-Ni-Cu |
- | - | CuA111Ni6Fe5 (2.0978) | - | Al-Fe-Ni-Cu |
- | - | CuA19Ni3Fe2 (2.0971) | - | Al-Fe-Mn-Ni-Cu |
- | - | - | C6161 | Al-Fe-Mn-Ni-Cu |
- | - | - | C6280 | Al-Fe-Mn-Ni-Cu |
BrAJNMc9−4-4−1 | C63200 | - | C6301 | Al-Fe-Mn-Ni-Cu |
- | C63800 | - | - | Al-Si-Co-Cu et Al-Si-Ni-Cu |
- | C64400 | - | - | Al-Si-Co-Cu et Al-Si-Ni-Cu |
Bronzes au béryllium :
Qualité bronze | Analogue américain | Bronze d’Allemagne | Analogique Japon |
---|---|---|---|
- | C17410 | - | - |
- | C17510 | CuNi2Be (2.0850) | - |
- | C17500 | CuCo2Be (2.1285) | - |
- | C17000 | CuBe1.7 (2.1245) | C1700 |
BrB2 | C17200 | CuBe2 (2.1447) | C1720 |
- | - | CuBe2Pb (2.1248) | - |
BrBET1.9 | - | - | - |
BrBNT1.9Mg | - | - | - |
Bronzes siliceux
Qualité du bronze | Analogie avec les États-Unis | Identique à l’Allemagne | Identique au Japon |
---|---|---|---|
- | - | CuNi1,5Si (2,0853) | - |
- | C64700 | - | - |
BrKH1−1 | - | CuNi2Si (2.0855) | - |
- | - | CuNi3Si (2.0857) | - |
- | C70250 | - | - |
- | C65100 | - | - |
BrKMZ3−1 | - | - | - |
Idem | C65500 | - | - |
Bronze au manganèse
Qualité bronze | Analogie avec les États-Unis | Identique à l’Allemagne | Japon analogue |
---|---|---|---|
BrMz5 | - | - | - |
Le bronze au tellure dans GOST 18175 n’a pas de désignation spéciale.
Tableau 2. Composition chimique des bronzes sans étain (GOST 18175−78) (fraction de masse, %)
Marque | Limite de la teneur en éléments | Cu | Ag | Al | Be | Cd | Cr | Fe | Mg | Mn | Ni | P | Pb | Si | Sn | Te | Ti | Zn | Somme des autres éléments |
---|---|---|---|---|---|---|---|---|---|---|---|---|---|---|---|---|---|---|---|
BrA5 | min. | ost. | - | 4,0 | - | - | - | - | - | - | - | - | - | - | - | - | - | - | - |
BrA5 | max. | - | - | 6,0 | - | - | - | 0,5 | - | 0,5 | - | 0,01 | 0,03 | 0,1 | 0,1 | - | - | 0,5 | 1,1 |
BrA7 | min. | ost. | - | 6,0 | - | - | - | - | - | - | - | - | - | - | - | - | - | - | - |
BrA7 | max. | - | - | 8,0 | - | - | - | 0,5 | - | 0,5 | - | 0,01 | 0,03 | 0,1 | 0,1 | - | - | 0,5 | 1,1 |
BrAMZ9−2 | min. | ost. | - | 8,0 | - | - | - | _ | - | 1,5 | - | - | - | - | - | - | - | - | - |
БрАМц9−2 | max. | - | - | 10,0 | - | - | - | 0,5 | - | 2,5 | - | 0,01 | 0,03 | 0,1 | 0,1 | - | - | 1,0 | 1,5 |
BrAmc10−2 | min. | ost. | - | 9,0 | _ | - | - | _ | - | 1,5 | - | - | - | - | - | - | - | - | - |
БрАМц10−2 | max. | - | - | 11,0 | - | - | - | 0,5 | - | 2,5 | - | 0,01 | 0,03 | 0,1 | 0,1 | - | - | 1,0 | 1,7 |
BrAJ9−4 | min. | ost. | - | 8,0 | - | - | - | 2 | - | - | - | - | - | - | - | - | - | - | - |
BrAJ9−4 | max. | - | 10,0 | - | - | - | 4 | - | 0,5 | - | 0,01 | 0,01 | 0,1 | 0,1 | - | - | 1 | 1,7 | |
BrAJMc10−3-1,5 | min. | ost. | - | 9,0 | - | - | - | 2 | - | 1,0 | - | - | - | - | - | - | - | - | - |
BrAJMc10−3-1.5 | max. | - | 11,0 | - | - | - | 4 | - | 2,0 | - | 0,01 | 0,03 | 0,1 | 0,1 | - | - | 0,5 | 0,7 | |
BrAJN10−4-4 | min. | ost. | - | 9,5 | - | - | - | 3,5 | - | - | 3,5 | - | - | - | - | - | - | - | - |
BrAJHN10−4-4 | max. | - | - | 11,0 | - | - | - | 5,5 | - | 0,3 | 5,5 | 0,01 | 0,02 | 0,1 | 0,1 | - | - | 0,3 | 0,6 |
BrAJNMc9−4-4−1 | min. | ost. | - | 8,8 | - | - | - | 4 | - | 0,5 | 4,0 | - | - | - | - | - | - | - | - |
БрАЖНМц9−4-4−1 | max. | - | - | 11,0 | - | - | - | 5 | - | 1,2 | 5,0 | 0,01 | 0,02 | 0,1 | 0,1 | - | - | 0,5 | 0,7 |
BrB2 | min. | ost. | - | - | 1,8 | - | - | - | - | - | 0,2 | - | - | - | - | - | - | - | - |
BrB2 | max. | - | - | 0,2 | 2,1 | - | - | 0,15 | - | - | 0,5 | - | 0,05 | 0,15 | - | - | - | - | 0,5 |
BrBNT1.9 | min. | ost. | - | - | 1,85 | - | - | - | - | 0,2 | - | - | - | - | - | 0,10 | - | - | |
BrBNT1.9 | max. | - | - | 0,2 | 2,1 | - | - | 0,15 | - | - | 0,4 | - | 0,05 | 0,15 | - | - | 0,25 | - | 0,5 |
BrBNT1.9Mg | min. | ost. | - | - | 1,85 | - | - | - | 0,07 | - | 0,2 | - | - | - | - | - | 0,10 | - | - |
BrBNT1.9Mg | max. | - | - | 0,2 | 2,1 | - | - | 0,15 | 0,13 | - | 0,4 | - | 0,05 | 0,15 | - | - | 0,25 | - | 0,5 |
Tableau 3. Propriétés caractéristiques et types de produits semi-finis en bronzes sans étain
Nuance de bronze | Propriétés spécifiques | Types de produits semi-finis |
---|---|---|
БрАМц9−2 | Haute résistance sous charges alternées | Barres, bandes, barres, fils, pièces forgées |
БрАЖ9−4 | Propriétés mécaniques élevées, bonnes propriétés de glissement, résistance à la corrosion | barres, tubes, pièces forgées |
BrAJMZ10−3-1.5 | Mauvaise déformabilité à froid, déformable à chaud, haute résistance à des températures élevées, résistant à la corrosion, haute résistance à l'érosion et à la cavitation | barres, tubes, fils, pièces forgées |
BrAJHN10−4-4 | Mal déformé à froid, se déforme à chaud, haute résistance aux températures élevées, résistant à la corrosion, haute résistance à l'érosion et à la cavitation | barres, tubes, pièces forgées |
BrB2, BrBNT1.9 | résistance élevée et résistance à l’usure, propriétés élastiques élevées, bonnes propriétés de glissement, conductivité électrique et thermique moyenne, très bonne déformabilité à l'état trempé | Bandes, feuillards, barres, tubes, fils |
BrKMZ3−1 | très résistant à la corrosion, soudable, résistant à la chaleur, haute résistance à la compression | Feuilles, bandes, rubans, barres, fils |
BrKN1−3 | Propriétés mécaniques et technologiques élevées, résistant à la corrosion, bonnes propriétés de glissement | Feuilles, bandes, bandes, barres, fils |
Fig. 1. Diagramme d'état du système (état d'équilibre)
Le diagramme montre que la solubilité maximale de l’aluminium à l'état solide est de 9,4% (en masse). En augmentant la température de 565 °C à 1037 °C, la solubilité de l’aluminium dans le cuivre diminue et atteint 7,5%.
Les phases stables du système Cu-Al comprennent les phases α, β, γ2 et α2.
La phase α est la solution solide primaire, isomorphe, avec un réseau cristallin cubique élémentaire à faces centrées. Lors du refroidissement lent de l’alliage à 400 °C, la phase α forme un quasi-ordre, ce qui entraîne une réduction marquée de sa résistivité électrique, qui se poursuit en dessous de 200 °C en raison de l'élimination des défauts d’empilement.
La phase β est une solution solide formée à partir de la composition stœchiométrique de Cu3Al directement à partir de la fusion à 1036−1079 °C, avec un réseau cristallin cubique centré élémentaire. La phase β est ductile, conductrice d'électricité et stable à des températures supérieures à 565 °C. Lorsque l’alliage refroidit rapidement (à une vitesse >2°C/min), il subit des transformations abruptes de type martensite formant des phases intermédiaires (Figure 1). Lors d’un refroidissement lent (2°C/min), la phase β se désintègre en eutectoïde α+γ2 pour former la phase γ2 à gros grains qui émerge sous forme de chaînes continues, ce qui confère à l’alliage sa fragilité. La phase γ2 (Cu9Al4), formée à partir de la phase γ', est stable à basse température, cassante et dure, avec une conductivité électrique inférieure à celle de la phase β.
La phase α2, formée à 363 °C à la suite d’une réaction peritectoïdale entre les phases α et γ2, présente un réseau cristallin cubique à faces centrées, mais avec des paramètres différents.
Les phases métastables dans les alliages: β1 — avec un réseau cristallin cubique centré élémentaire (a — 5,84 Å, Al — 11,9%), ordonné; β' — avec un réseau cristallin cubique centré élémentaire (Al — 11,6%), très déformé; β1' — avec un réseau cristallin rhombique élémentaire (a = 3.67 Å, c = 7.53 Å, Al — 11.8%), ordonné; Phase γ1 avec cellule unitaire orthorhombique (a = 4,51 Å, c = 5,2 Å, c = 4,22 Å, Al — 13,6%), ordonnée. L’existence d’autres phases, qui sont une variation de la phase β1', est supposée.
La détermination de la structure des alliages Cu-Al est difficile. Des vitesses de refroidissement très élevées (1 à 8°C/min, selon la teneur en aluminium) sont nécessaires pour obtenir des structures d’alliage équilibrées. Ces structures sont révélées en attaquant les alliages avec du chlorure ferrique.
Cependant, l’attaque au chlorure ferrique ne permet pas toujours de déterminer avec certitude les phases des alliages refroidis à la vitesse normale. Dans ce cas, des techniques spéciales utilisant le polissage électrolytique sont utilisées pour révéler la véritable structure des alliages Cu-Al.
La structure des alliages duals cuivre-aluminium et des bronzes multicomposants basés sur le système cuivre-aluminium à l'état d'équilibre est définie par un diagramme d'état (Fig. 2).
Fig. 2. Diagramme de transformation de phase pour un bronze d’aluminium avec une teneur en aluminium de 12,07% (en masse)
Cependant, dans les conditions de production, lors de la coulée des lingots et des billettes et de leur traitement sous pression à chaud et à froid, les vitesses de refroidissement et de chauffage diffèrent considérablement de celles auxquelles le diagramme d'état d'équilibre est construit.
Par conséquent, les structures des produits semi-finis coulés et déformés diffèrent également de celles déterminées par le diagramme d'état d'équilibre.
Pour déterminer les propriétés et la microstructure des alliages à l'état métastable, on trace des courbes C qui montrent la cinétique de la transformation de phase en fonction de la vitesse de refroidissement et des temps de maintien isotherme à des températures inférieures à la température de transformation eutectoïde.
Les alliages monophasés (bronzes α-aluminium) sont ductiles et faciles à travailler sous pression, les alliages biphasés (bronzes α+γ2-aluminium) à forte teneur en aluminium sont moins ductiles et principalement utilisés comme alliages de fonderie.
Il convient de noter que la teneur réelle en aluminium dans les alliages industriels varie considérablement, ce qui affecte la stabilité des propriétés mécaniques des demi-produits en bronze d’aluminium coulé et déformé.
L'évolution des propriétés mécaniques des bronzes d’aluminium traités par pression (résistance à la traction σv, proportionnalité σnu et limite d'élasticité σ0,2, allongement relatif δ et contraction ψ, résilience an (TC) et dureté Brinell (HB) en fonction de la teneur en aluminium, comme le montre la Fig.3.
Figure 3: Variation des propriétés mécaniques des bronzes d’aluminium Cu-Al en fonction de la teneur en aluminium :
a — bandes déformées de 40% et recuites à 650oC pendant 30 min ;
b — barres et tubes pressés en bronze d’aluminium BrAJMc10−3-1,5
Cette caractéristique des bronzes d’aluminium est utilisée dans les normes nationales étrangères (États-Unis, Allemagne, Royaume-Uni, France, etc.). Dans ces pays, un intervalle plus étroit de la teneur en aluminium dans les bronzes est utilisé pour améliorer les propriétés mécaniques, qui est environ 1,5 à 2 fois moins que dans les bronzes similaires utilisés dans les pays de la CEI (voir les alliages GOST 493, GOST 17328 et leurs analogues étrangers).
Aux États-Unis, en France et au Japon, il existe des groupes de bronzes de type BrAJMc, dans lesquels les propriétés mécaniques requises ne sont obtenues qu’en modifiant la teneur en aluminium.
Effet des éléments d’alliage sur les propriétés des bronzes d’aluminium
L’alliage des bronzes d’aluminium à deux composants avec différents éléments entraîne une modification marquée de leurs propriétés. Les principaux éléments d’alliage dans les alliages Cu-Al sont le fer, le manganèse et le nickel. Les bronzes d’aluminium ont généralement des teneurs en fer et en nickel ne dépassant pas 5,5, le manganèse 3% (en masse).
Le fer à l'état solide est légèrement soluble dans les alliages Cu-Al et forme avec l’aluminium un composé intermétallique de Fe3Al, qui se distingue comme une phase indépendante sous forme de fines particules. À environ 1% de Fe dans les alliages, un petit nombre de particules fines se forment, situées près de la région eutectoïde (α + γ2) et l’encadrant. Cependant, avec l’augmentation de la teneur en fer, leur nombre augmente. Ainsi, à 4% de Fe, les particules Fe3Al finement dispersées sont formées à la fois dans la région α + γ2, et dans la région α. Les particules finement dispersées du composé intermétallique Fe3Al inhibent la croissance des grains dans les bronzes d’aluminium à haute température. Sous l’influence du fer, qui améliore considérablement les propriétés mécaniques et retarde la température de recristallisation, le phénomène dit de «recuit spontané", qui entraîne une fragilité accrue des alliages, disparaît dans les bronzes d’aluminium. Le fer, en affinant la structure, arrête la formation, dans les alliages Cu-Al contenant 8,5−11,0% d’Al, d’une phase γ2 à gros grains, qui se présente sous forme de chaînes continues, ce qui entraîne une fragilité.
Le fer, en fonction de sa teneur dans l’alliage, affecte la structure, les transformations de phase et les propriétés des bronzes d’aluminium de la manière suivante: jusqu'à 1,2%, il est en solution solide (phase α), et à des concentrations plus élevées, il est isolé sous forme d’inclusions globulaires individuelles qui, dans les alliages doubles et triples contenant du nickel,.sont généralement représentées par la phase k. La composition approximative de la phase k est de 85% Cu, 10% Al et 5% Fe; à une teneur en alliage de 1,2 à 5,5%, le fer a un fort effet modificateur sur le changement de grain primaire dans les billettes coulées; à une teneur > 5,5% Fe, cet effet disparaît. C’est pourquoi les bronzes d’aluminium industriels n’ont normalement pas une teneur en fer supérieure à 4%.
Le fer durcit les bronzes d’aluminium en augmentant la résistance de la solution solide (phase α) et en séparant la phase k. Les alliages à forte teneur en fer, comme le BrAZh10−10, sont plus résistants à l’abrasion et à l'érosion, mais moins résistants à l’eau de mer.
Un alliage supplémentaire des alliages Cu-Al-Fe avec du manganèse et du nickel augmente de manière significative leur solidité et leur résistance à la corrosion et modifie la structure et la composition de la phase k.
Lemanganèse se dissout bien dans les bronzes d’aluminium à l'état solide. À une teneur en Mn > 2% dans les alliages du système Cu-Al, la transformation de la phase α + γ2 en phase β est considérablement accélérée (le manganèse abaisse la température eutectoïde et retarde la décomposition de la phase β); à une teneur en Mn > 8%, la décomposition de la phase β n’a pratiquement pas lieu.
Une particularité des ajouts de manganèse aux bronzes d’aluminium est également l’apparition de noyaux d’aiguilles de la phase β pendant le refroidissement avant que la phase β ne se transforme en α+ γ2.
L’apparition de germes d’aiguilles en phase α est particulièrement visible lors du recuit de grands produits semi-finis. C’est pourquoi des bronzes spéciaux aluminium-manganèse à haute teneur en manganèse sont largement utilisés pour couler des hélices dont l'épaisseur varie de 15 à 400 mm.
Dans les bronzes de types БрАЖ10−4, БрАЖ9−4, le manganèse est l'élément principal qui détermine la cinétique de la transformation de la phase β lors du chauffage et qui améliore sa trempabilité en profondeur. La teneur en Mn dans ces bronzes est autorisée jusqu'à 1,5%. Mais lorsque la teneur en Mn passe de 2 à 5%, la dureté des bronzes d’aluminium après une trempe à 800−1000°C diminue. Par conséquent, pour augmenter la dureté des bronzes d’aluminium pendant le traitement thermique, ils ne doivent pas contenir plus de 0,5% de Mn.
Le manganèse augmente les propriétés mécaniques et de corrosion et améliore les caractéristiques technologiques des alliages Cu-Al. Les bronzes d’aluminium alliés au manganèse se caractérisent par une résistance accrue à la corrosion, une résistance au froid et une grande déformabilité à chaud et à froid.
Lenickel, qui est insoluble dans le cuivre à l'état solide, est presque insoluble dans l’aluminium (la solubilité à 560 °C est de 0,02%). Le nickel augmente la région de la phase α dans les systèmes Cu-Al et Cu-Al-Fe. Dans les alliages Cu-Al-Ni, le nickel entraîne un déplacement significatif de la zone de solution solide vers l’angle du cuivre lorsque la température diminue, ce qui permet de les durcir par dispersion. La capacité de durcissement par dispersion de ces alliages se situe à 1% de Ni. Le nickel augmente la température de décomposition eutectoïde de β en α+γ2 à 615 °C et inhibe la conversion de α+γ2 en β lors du chauffage. L’effet du nickel devient particulièrement sensible à sa teneur supérieure à 1,5%. Ainsi, avec 2% de Ni, la phase β apparaît à 790 °C et avec 4% de Ni à 830 °C.
Le nickel a un effet favorable sur la structure de l’eutectoïde α+γ2 et du pseudo-eutectoïde α + β, augmente significativement la résistance aux transformations de phase de la phase β et favorise, lors de la coulée et de la trempe, une plus grande quantité de phase β'- métastable de type martensitique. Dans ce cas, la phase α devient plus arrondie, la structure devient plus uniforme et la dispersion de l’eutectoïde augmente.
L’alliage au nickel des bronzes d’aluminium augmente sensiblement leurs propriétés physiques et mécaniques (conductivité thermique, dureté, résistance à la fatigue), leur résistance au froid et leurs caractéristiques antifriction, leur résistance à la corrosion et à l'érosion dans l’eau de mer et les solutions d’acide chlorhydrique faible, leur résistance à la chaleur et leur température de recristallisation, sans détérioration notable des caractéristiques technologiques. Dans les alliages avec le nickel, l’effet modificateur du fer est considérablement accru.
Les bronzes d’aluminium du système Cu-Al-Ni sont rarement utilisés. Le nickel est généralement ajouté aux bronzes d’aluminium en combinaison avec d’autres éléments (principalement le fer). Les bronzes d’aluminium de type БрАЖН10−4-4 sont les plus répandus. Les propriétés optimales de ces bronzes sont obtenues avec un rapport Fe: Ni = 1:1. À un rapport de 3% Ni et 2% Fe dans ces bronzes, la phase k peut apparaître sous deux formes: sous forme de petites inclusions rondes de solution solide à la base du fer, allié à l’aluminium et au nickel, et sous forme de plaques minces, de composition intermétallide NiAl.
Les bronzes d’aluminium déformés les plus utilisés appartiennent aux systèmes suivants: Cu-Al, Cu-Al-Fe, Cu-Al-Mn, Cu-Al-Fe-Mn, Cu-Al-Fe-Ni.
Les bronzes d’aluminium sont très résistants à la corrosion dans les solutions de dioxyde de carbone, ainsi que dans les solutions de la plupart des acides organiques (acétique, citrique, lactique et autres), mais ils sont instables dans les acides minéraux concentrés. Dans les solutions de sels sulfuriques et d’alcalis caustiques, les bronzes d’aluminium monophasés à teneur réduite en aluminium sont plus stables.
Les bronzes d’aluminium sont moins sensibles à la fatigue par corrosion que d’autres matériaux.
Particularités de l’usinage des bronzes d’aluminium corroyés
Afin d’obtenir des demi-produits déformables homogènes présentant des propriétés mécaniques améliorées et une résistance élevée à la fatigue, il est recommandé de couler les bronzes d’aluminium en continu et d’effectuer le traitement ultérieur selon une méthode spéciale comprenant les opérations suivantes
a) usinage à chaud de la billette coulée avec sertissage total jusqu'à 30% ;
b) traitement thermique à une température donnée (t0) avec un écart de ± 2 °C (chauffage à une température donnée, délai de 20 minutes tous les 25 mm de la section transversale du matériau) ;
c) le revenu dans l’eau ou l’huile à 600 °C ;
d) traitement à chaud sous pression à une température inférieure de 35−50°C à celle adoptée pour l'étape de traitement thermique «b» en fonction de la teneur en aluminium de l’alliage (la teneur en aluminium doit être définie avec une précision de ±0,02%). La température de traitement thermique est déterminée par la formule empirique :
t=(1990 — 1000A)°C,
où A est la teneur en aluminium de l’alliage, en % (en masse).
La relation graphique entre la température et la teneur en aluminium pour le traitement thermique et le second traitement thermique sous pression des bronzes d’aluminium est illustrée à la Fig. 4.
Fig. 4. Dépendance de la température sur la teneur en aluminium dans le traitement thermique et le traitement thermique sous pression des bronzes d’aluminium :
1 — température du traitement thermique ;
2 — température du travail à chaud sous pression
Bronzes au béryllium (alliages cuivre-béryllium)
Les bronzes au béryllium sont des alliages uniques en raison de la combinaison favorable de bonnes propriétés mécaniques, physico-chimiques et anticorrosives. Ces alliages, après trempe et amélioration, présentent une résistance à la traction, une élasticité, une fluidité et une résistance à la fatigue élevées, sont hautement conducteurs, conducteurs de chaleur, durs, ont une résistance élevée au fluage, une résistance cyclique élevée avec une hystérésis minimale, une résistance élevée à la corrosion et à la fatigue due à la corrosion. Ils sont résistants au gel, non magnétiques et ne produisent pas d'étincelles en cas d’impact. Les bronzes au béryllium sont donc utilisés pour la fabrication de ressorts et de pièces de ressorts pour des applications critiques, y compris les diaphragmes et les composants d’horlogerie.
Fig. 5. Diagramme d'état du système Cu-Be
Le diagramme montre que le cuivre et le béryllium forment une série de solutions solides. La région de solution solide α atteint 2,7% (en masse) à 864 °C. Avec la diminution de la température, la limite de solubilité de la région α se déplace assez nettement vers le cuivre. Elle est de 1,55% à 608 °C (transformation eutectoïde) et tombe à 0,2% à 300 °C, ce qui indique que les bronzes au béryllium peuvent être enrichis.
Un changement significatif de la concentration de béryllium dans la solution α-solide avec la diminution de la température favorise le durcissement par dispersion des alliages Cu-Be. L’effet du durcissement par dispersion des alliages Cu-Be sur la teneur en béryllium est illustré à la figure 6.
Figure 6. Influence de la teneur en béryllium sur l’effet de durcissement par dispersion des alliages Cu-Be: 1 — durcissement à 780 °C; 2 — durcissement à 780 °C + revenu à 300 °C
Les bronzes au béryllium subissent un traitement thermique à 750−790°C suivi d’une trempe dans l’eau pour produire une solution solide sursaturée. Dans cet état, les bronzes au béryllium peuvent être facilement pliés, étirés et autres déformations. La deuxième opération du traitement thermique — le revenu — est effectuée à une température de 300−325°C. La phase β'- est libérée. Ces émissions sont associées à des contraintes de réseau importantes qui augmentent la dureté et la résistance des alliages.
La transformation eutectoïde de la phase β à des températures inférieures à 608 °C aboutit à la formation de l’eutectoïde α + β'. La phase α a un réseau cubique à faces centrées dont le paramètre diminue avec l’augmentation de la teneur en béryllium. La phase β présente un réseau cubique centré avec un arrangement désordonné des atomes. La structure cristalline de la phase β est la même que celle de la phase β, mais elle présente un arrangement ordonné des atomes de béryllium.
Dans la pratique, les alliages binaires cuivre-béryllium sont rarement utilisés, les alliages à trois ou plusieurs composants étant très répandus.
Afin de ralentir les processus de transformation de phase et de recristallisation et d’obtenir une structure plus homogène, du nickel ou du cobalt ainsi que du fer sont ajoutés aux alliages Cu-Be. La teneur totale en nickel, cobalt et fer dans les bronzes au béryllium varie de 0,20 à 0,60% (en masse), y compris le nickel et le cobalt de 0,15 à 0,35% (en masse).
L’introduction de titane dans les alliages Cu-Be, qui forme une phase de durcissement avec le béryllium, contribue à ralentir les processus de diffusion dans ces alliages. Le titane, en tant qu'élément actif en surface, réduit la concentration de béryllium aux joints de grains et réduit le taux de diffusion dans ces zones. Dans le bronze au béryllium additionné de titane, on observe une décomposition homogène et, par conséquent, un durcissement plus uniforme.
Les propriétés du bronze au béryllium sont plus favorablement influencées par le titane en présence de nickel. L’ajout de titane et de nickel permet de réduire la teneur en béryllium des alliages à 1,7−1,9% (en masse).
Dans les alliages Cu-Be, le manganèse peut remplacer partiellement le béryllium sans réduction notable de la résistance. Les alliages Cu + 1% Be + 5−6% Mn et Cu + 0,5% Be + 10% Mn après durcissement par précipitation ont des propriétés mécaniques similaires à celles du bronze au béryllium BrB2.
Les additifs de magnésium en petites quantités (0,1%) augmentent l’effet du durcissement par dispersion du bronze au béryllium et, dans la gamme de 0,1 à 0,25%, réduisent sensiblement sa plasticité.
Le plomb, le bismuth et l’antimoine sont des impuretés très nocives pour les bronzes au béryllium, qui nuisent à leur déformabilité à chaud.
Dans les alliages standard Cu-Be, la teneur en Al et Si ne doit pas dépasser 0,15% de chaque élément. À de telles concentrations, ces éléments n’altèrent pas les propriétés des alliages.
Bronzes au manganèse
Les bronzes au manganèse se caractérisent par des propriétés mécaniques élevées. Ces alliages présentent une excellente aptitude à la déformation à chaud et à froid, avec une déformation par laminage à froid pouvant aller jusqu'à 80%.
Les bronzes au manganèse sont résistants à la corrosion et à la chaleur et sont donc utilisés dans la fabrication de pièces et de produits fonctionnant à des températures élevées. En présence de manganèse, la température de recristallisation du cuivre augmente de 150 à 200 °C.
Fig. 7. Diagramme d'état du système Cu-Mn
À des températures élevées, le manganèse est soluble sans restriction dans le cuivre, tant à l'état liquide qu'à l'état solide. Dans un alliage contenant 36,5% de magnésium (en masse), les températures du liquidus et du solidus du système sont identiques et s'élèvent à 870 ± 5 °C. Avec la diminution de la température, une série de transformations a lieu et de nouvelles phases se développent. La surface y de la solution solide diminue avec la température. Les bronzes au manganèse contenant moins de 20% de magnésium sont monophasés dans la plage de température allant de la température ambiante au point de fusion. La figure 8 montre la dépendance des propriétés mécaniques des bronzes au manganèse par rapport à la teneur en manganèse.
Figure 8. Évolution des propriétés mécaniques des alliages Cu-Mn en fonction de la teneur en manganèse: a — limite d'élasticité σ0,2; b — résistance à la traction σb; c — allongement relatif δ
Le bronze le plus utilisé est le BrMc5, qui se déforme bien à chaud et à froid, présente une résistance élevée à la corrosion et conserve ses propriétés à des températures élevées.
Bronzes au silicium
Les bronzes au silicium présentent d’excellentes propriétés mécaniques, de roulement à ressort et d’antifriction, et sont résistants à la corrosion et à l’usure. Ces alliages présentent une excellente aptitude à l’usinage à chaud et à froid sous pression, peuvent être soudés à l’acier et sont soudables avec de la brasure tendre et dure. Ils sont non magnétiques, résistants aux chocs et ne perdent pas leur ductilité à très basse température.
Diagramme d'état de l’alliage Cu-Si :
Figure 9. Diagramme d'état du système Cu-Si
Comme le montre le diagramme, la limite de la solution solide α atteint 5,4% de Si (en masse) à 830oC et se déplace vers le cuivre à mesure que la température diminue. La phase α a un réseau cubique à faces centrées avec un paramètre a=(3.6077+0.00065k) Å, où k est la concentration de silicium, %.
À une température > 577 oC, une nouvelle phase avec un réseau hexagonal dense (a=2,5550 Å, c=4,63644 Å) apparaît à droite de la limite entre la solution α et la solution solide. La caractéristique distinctive de la phase k est le changement de couleur perceptible en lumière polarisée, qui passe d’un brun clair à un brun foncé. À 557o C, la transformation de phase k → α+ γ se produit.
La nature du changement de silicium dans la solution α-solide avec la diminution de la température indique que certains alliages du système Cu-Si peuvent être enrichis. Cependant, l’effet du durcissement par dispersion des alliages est faible et n’est pas appliqué dans la pratique.
Les bronzes au silicium additionnés de manganèse et de nickel sont les plus courants. Les bronzes bicomposants additionnés d'étain, de zinc, de fer et d’aluminium sont moins utilisés.
L’alliage des bronzes cuivre-silicium avec du manganèse améliore considérablement leurs propriétés mécaniques et leur résistance à la corrosion.
Diagramme d'état du système Cu-Si-Mn :
Figure 10. Diagramme d'état du système Cu-Si-Mn. Isotherme de saturation de la région de la solution solide
Malgré le déplacement de la limite de la région α avec la diminution de la température vers le coin du cuivre, l’effet d’ennoblissement des alliages Cu-Si-Mn est faiblement prononcé.
Les additifs de nickel augmentent considérablement les propriétés mécaniques des bronzes au silicium. Le silicium et le nickel forment un composé intermétallique (Ni2Si) qui est nettement soluble dans le cuivre. La solubilité du Ni2Si dans le cuivre diminue fortement avec la baisse de la température (de 900 à 500°C) et les particules précipitées du composé intermétallique durcissent les alliages. Le traitement thermique (trempe, vieillissement) peut augmenter la résistance et la dureté de ces alliages de près de 3 fois par rapport aux alliages recuits. Après trempe, les alliages Cu-Si-Ni présentent une ductilité élevée et sont parfaitement usinables à froid.
L'évolution de la résistance à la traction de ces alliages dépend de la teneur en Ni2Si et de la méthode de traitement thermique :
Figure 11. Évolution de la résistance des alliages Cu-Ni-Si en fonction de la teneur en Ni2Si et de la méthode de traitement thermique: 1 — trempe à 900−950°C; vieillissement à 350−550°C; 2 — recuit à 800 °C; 3 — trempe à 900−950°C.
Les additifs de cobalt et de chrome ont le même effet sur les bronzes au silicium que le nickel, mais l’effet de durcissement par dispersion des alliages sous l’influence des siliciures de cobalt et de chrome est beaucoup plus faible.
L’ajout de petites quantités de Sn (jusqu'à 0,5%) augmente sensiblement la résistance à la corrosion des bronzes au silicium, tandis que le fer la réduit. C’est pourquoi, dans les bronzes au silicium traités par pression, la teneur en fer ne doit pas dépasser 0,2−0,3% (en masse).
L’ajout de Zn dans une fourchette de 0,5% à 1,0% dans la fusion des bronzes au silicium améliore leurs propriétés technologiques.
L’alliage des bronzes au silicium avec l’aluminium augmente leur résistance et leur dureté, mais les alliages Cu-Si-Al ne sont pas très répandus en raison de leurs mauvaises propriétés de soudage et de brasage.
L’arsenic, le phosphore, l’antimoine, le soufre et le plomb sont des impuretés nocives dans les bronzes au silicium traités sous pression.
Propriétés anticorrosion des bronzes au silicium
Les bronzes au silicium possèdent une excellente résistance à la corrosion sous l’influence de l’atmosphère marine, industrielle et rurale, de l’eau douce et de l’eau de mer (à un débit de 1,5 m/sec), des solutions concentrées chaudes et froides d’acides alcalins et sulfuriques et des solutions froides d’acides chlorhydriques et organiques, des chlorures et des sulfates de métaux légers. Ils sont assez stables dans l’atmosphère de gaz secs: chlore, brome, fluor, sulfure d’hydrogène, fluorure et chlorure d’hydrogène, gaz sulfurique et ammoniac, mais ils se corrodent dans ces milieux en présence d’humidité.
Cependant, les bronzes au silicium sont peu résistants à l’hydroxyde d’aluminium, aux chlorures et aux sulfates de métaux lourds. Ils se corrodent rapidement dans les eaux minières acides contenant du Fe2 (S04)3, ainsi que dans les solutions de sels d’acide chromique.
Particularités du traitement thermique des bronzes siliceux
Le recuit léger des bronzes siliceux (y compris le chauffage et le refroidissement) doit être effectué à la vapeur d’eau. Les pellicules d’oxyde qui se forment à la surface des produits semi-finis au cours du recuit sont facilement éliminées par décapage à température ambiante dans une solution d’acide sulfurique à 5%.
Bronzes d'étain
Les bronzes à l'étain sont des alliages de compositions différentes basés sur le système Cu-Sn. La liste récapitulative des bronzes à l'étain russes traités sous pression et de leurs alliages analogues étrangers est présentée dans le tableau 4.
Liste récapitulative des bronzes d'étain russes traités sous pression et de leurs équivalents étrangers
Bronzes phosphorescents à l'étain :
Marque du bronze national | Analogue américain | Analogique allemand | Analogique Japon |
---|---|---|---|
BrOF2−0,25 | - | - | - |
BrOF4−0,25 | С51100 | CuSn4 (2.1016) | C5111 |
- | C53400 | - | - |
BrOF6,5−0,15 | - | CuSn6 (2.1020) | C5191 |
- | C51000 | - | - |
- | C53200 | - | - |
BrOF6,5−0,4 | - | - | - |
BrOF7−0,2 | - | SuSn6 (2.1020) | C5210 |
BrOF7−0,2 | - | SuSn8 (2.1030) | - |
BrOF8.0−0.3 | C52100 | Idem | C5212 |
- | C52400 | - | - |
Bronzes étain-zinc :
Qualité de bronze domestique | Analogue américain | Identique à celle de l’Allemagne | Japon analogue |
---|---|---|---|
BrOC4−3 | - | - | - |
- | - | CuSn6Zn6 (2.1080) | - |
Bronzes étain-nickel :
Qualité de bronze domestique | Analogique américain | Analogique Allemagne | Japon analogique |
---|---|---|---|
- | C72500 | CuNi9Sn2 (2.0875) | - |
- | C72650 | - | - |
- | C72700 | - | - |
- | C72900 | - | - |
Bronze étain-zinc-plomb :
Qualité de bronze domestique | Analogue américain | Identique à celle de l’Allemagne | Japon analogue |
---|---|---|---|
BrOZS4−4-2,5 | - | - | - |
- | С54400 | - | - |
BrOtzS4−4-4 | - | - | - |
Le diagramme d'état du système Cu-Sn est présenté dans la figure 12.
Figure 12 Diagramme d'état du système Cu-Sn
La phase α-solide de l'étain dans le cuivre (réseau cubique à faces centrées) est malléable à chaud et à froid.
Les phases β et γ ne sont stables qu'à des températures élevées et se désintègrent à des taux élevés lorsque la température diminue. La phase δ (Cu31Sn8, phase γ du réseau) — produit de la décomposition de la phase γ (ou β') à 520 °C est dure et cassante.
La décomposition de la phase δ en α + Cu3Sn (phase ε) commence à 350 °C. Lorsque la température diminue, la décomposition de la phase δ se fait extrêmement lentement (70−80% lors d’un recuit long après déformation à froid). En pratique, dans les alliages contenant jusqu'à 20% d'étain, la phase ε est absente.
Dans les bronzes techniques à l'étain, la teneur en étain varie de 2% à 14%, plus rarement jusqu'à 20%.
Les alliages du système Cu-Sn, en fonction de la teneur en étain, se composent soit de cristaux homogènes de solution solide α, soit de cristaux α et eutectoïdes α + β.
Le processus de diffusion dans les bronzes à l'étain se déroule lentement. La structure dendritique ne disparaît qu’après plusieurs cycles de traitement thermomécanique. C’est pourquoi il est difficile de traiter les bronzes d'étain sous pression.
Les bronzes d'étain sont désoxydés par le phosphore pendant la fusion, ce qui explique que la plupart des alliages binaires Cu-Sn contiennent du phosphore résiduel. Le phosphore est considéré comme un additif d’alliage lorsque sa teneur dans l’alliage est supérieure à 0,1%.
Les principaux additifs d’alliage dans les bronzes à l'étain autres que le phosphore sont le plomb, le zinc et le nickel.
Effet des additifs d’alliage
Le phosphore en interaction avec le cuivre donne le composé chimique Cupr (14,1% P), qui forme un eutectique avec le cuivre à 714 °C (teneur en P — 8,4% (en masse)). Dans le système ternaire Cu-Sn-P, un eutectique ternaire se forme à 628 °C, contenant, %:80,7Cu, 14,8 Sn et 4,5P.
Le diagramme d'état du système Cu-Sn-P (Fig.13) montre que la limite de saturation de la solution α-solide se déplace fortement vers l’angle du cuivre avec l’augmentation de la teneur en étain et la diminution de la température.
Fig. 13. Diagramme d'état du système Cu-Sn-P: a — angle de cuivre; b — sections polymétriques du système Cu-Sn-P à teneur en étain constante.
Lorsque la teneur en P des bronzes à l'étain est supérieure à 0,3%, les inclusions eutectiques de phosphure sont les dernières à se manifester. Les bronzes d'étain à 0,5% de P et plus se cassent facilement lorsqu’ils sont déformés à chaud, car les eutectiques de phosphure fondent. Par conséquent, la teneur maximale en phosphore des bronzes d'étain traités sous pression est de 0,4 pour cent. Les bronzes d'étain ayant cette teneur en phosphore ont des propriétés mécaniques optimales, un module, une résistance à la traction et une résistance à la fatigue accrus. La déformabilité des bronzes d'étain à haute teneur en phosphore peut être améliorée par un recuit d’homogénéisation, après lequel une partie considérable du phosphore est transformée en solution α-solide.
De faibles ajouts de zirconium, de titane, de bore et de niobium améliorent également l’ouvrabilité à chaud et à froid des bronzes à l'étain.
Leplomb est pratiquement insoluble dans les bronzes à l'étain à l'état solide. Pendant la solidification de l’alliage, il est libéré en tant que phase indépendante sous la forme d’inclusions sombres entre les dendrites. Le plomb améliore considérablement la densité, le glissement et l’usinabilité des bronzes d'étain, mais réduit considérablement leurs propriétés mécaniques. Les bronzes d'étain antifriction contiennent jusqu'à 30% de plomb.
Lezinc est bien soluble dans les bronzes d'étain à l'état solide et, tout en modifiant légèrement la structure des alliages, il améliore sensiblement leurs propriétés technologiques.
Lenickel déplace la limite α de la solution solide vers l’angle du cuivre (fig.14).
Fig. 14. Diagramme d'état du système Cu-Sn-Ni: а — section de l’angle de cuivre à la teneur en nickel de 2%; b — région de la limite de saturation de la solution solide à température ambiante. Angle de cuivre.
Le réseau cristallin de la solution α-solide n’est pas modifié par le nickel, mais son paramètre augmente légèrement (-0,007 A). A de faibles concentrations d'étain, une nouvelle phase (Ni4Sn) apparaît dans la région hétérogène qui, selon la vitesse de solidification, émerge soit sous forme de petits cristaux en forme d’aiguilles (refroidissement rapide), soit sous forme d’inclusions bleu clair. Les liquides dans les alliages Cu-Sn augmentent sensiblement lorsqu’ils sont alliés au nickel. À 539 °C se produit la transformation eutectoïde de α + γ en α + β'. La phase δ' est polarisée, contrairement à la phase δ du système double Cu-Sn.
Le nickel augmente les propriétés mécaniques et la résistance à la corrosion des bronzes à l'étain, affine leur structure et, à une teneur de 1%, constitue un additif utile. À plus de 1% de Ni, bien que les alliages soient enrichis, leur usinabilité à la pression est compromise. Le nickel a un effet particulièrement dramatique sur les bronzes à l'étain. En revanche, à une teneur de 0,5−1%, le nickel n’influence ni la structure ni les propriétés des bronzes à l'étain et au zinc.
Effet des impuretés
Les impuretés d’aluminium, de magnésium et de silicium sont très nocives pour les bronzes à l'étain. Bien que ces éléments, qui font partie de la solution solide, puissent améliorer les propriétés mécaniques des bronzes, ils sont fortement oxydés pendant la fusion, produisant des oxydes réfractaires qui se placent le long des joints de grains, ce qui rompt la liaison entre eux.
Le bronze d'étain, qui peut être traité sous pression, est également affecté par l’arsenic, le bismuth, l’antimoine, le soufre et l’oxygène. Ce dernier réduit les propriétés antifriction des bronzes d'étain.
Propriétés anticorrosion
Les bronzes d'étain sont très résistants aux atmosphères (rurales, industrielles, marines). Ils sont plus résistants à l’eau de mer que le cuivre et le laiton (la résistance des bronzes à l’eau de mer augmente avec la teneur en étain). Le nickel augmente également la résistance à la corrosion des bronzes à l'étain dans l’eau de mer, tandis que le plomb, à des niveaux élevés, la réduit. Les bronzes à l'étain sont stables dans l’eau salée.
Les bronzes d'étain résistent de manière satisfaisante à la corrosion dans l’atmosphère de vapeur surchauffée à une température de 250 °C et à une pression ne dépassant pas 1,5 bar.À température ambiante, ils résistent également à la corrosion dans l’atmosphère de vapeur surchauffée à 250 °C, à une pression ne dépassant pas 2,0 MPa avec des solutions d’alcalis, de gaz secs (chlore, brome, fluor et leurs composés d’hydrogène, oxydes de carbone et de soufre, oxygène), de tétrachlorure de carbone et de chlorure d'éthylène.
Les bronzes d'étain sont instables en présence d’acides minéraux (nitrique, sulfurique) et gras, d’alcalis, d’ammoniaque, de cyanure, de composés de fer et de soufre, de gaz (chlore, brome, fluor) à haute température et d’eau d’exhaure acide.
La corrosion des bronzes d'étain sous l’action de l’acide sulfurique augmente en présence d’oxydants (K2Cu7, Fe2 (S04)3 etc.) et diminue de 10 à 15 fois en présence de 0,05% de benzylthiocyanate.
La vitesse de corrosion des bronzes à l'étain sous l’action d’un certain nombre d’agents est la suivante, en mm/an :
Alcalis :
à chaud… 1,52
à 293 K… 0,4−0,8
solutions d’ammoniaque à température ambiante… 1,27−2,54
acide acétique à température ambiante …0,025−0,6
H2S vapeur à 100 °C …1,3
dioxyde de soufre humide …2,5
vapeur d’eau sèche et humide (en fonction du débit) …0,0025−0,9
Les bronzes à l'étain sont sensibles à la corrosion fissurante sous l’action du nitrate de mercure.
Le laiton, le fer, le zinc et l’aluminium protègent les bronzes d'étain contre la corrosion électrochimique.